Ultrasonic Sensor Accuracy

Ultrasonic distance and level sensor accuracy is relatively easy to understand, but can be a difficult specification to achieve in a real-world application. The same principles apply to all ultrasonic level sensors—including Senix ToughSonic® sensors—no matter what is being measured.
To better explain how accuracy works, all potential environmental factors—such as temperature—should be removed. Accuracy specifications are generally determined indoors, in a controlled lab environment, under constant temperature and fixed conditions, and with no interference from factors such as wind or air movement.
Generally, specifications like “accuracy” are used to compare one sensor to another. Many published accuracy specifications are not clear or consistent with one another, and are difficult to compare, as some sensors have better features to help achieve better accuracy.
Accuracy, or absolute accuracy, is the difference between the output value being measured by the ultrasonic sensor and the actual target distance.
For example, an ultrasonic water level sensor reading a full-scale range of 12 feet (or 144 inches) will have an accuracy of ±0.144 inches at ambient temperature and controlled conditions. The same sensor reading a distance of 75 inches will have an accuracy of ±0.075 inches. This 0.1% detected accuracy is applicable whether the sensor is reading in distance level/volume (gallons).
The specification of accurate ultrasonic measurements depends on several physical parameters:
Air Temperature | Humidity | Air Pressure & Currents | Paint Mist | External Noise | Types of Gas | Tank Configurations & Dimensions | External Reference Targets
Air Temperature
Air temperature has the greatest impact on the measuring accuracy of an ultrasonic sensor, as its fluctuation affects the speed of an ultrasonic sensor’s pulse or sound waves.
As the temperature increases, sound waves travel faster to and from the target. Even though the target has not likely moved or shifted, it will appear that the target is closer.
Or, for a more detailed explanation: after the transit time of the reflected ultrasonic pulse has been measured, the sensor calculates the distance to the object using the speed of the sound. When sound is propagated in air, the speed of sound is about 344 m/s at room temperature. However, the speed of sound is temperature dependent and changes by approximately 0.17% with each degree Celsius. These changes affect the transit time and can distort the calculated distance.
Without temperature compensation, at a measuring distance of 100 cm, a 20°C change in temperature would cause a measurement error of -8.5 cm at 70°C and +7.65 cm at -25°C.
Most Senix ultrasonic sensors have a working range of -40°C to +70°C. All ToughSonic ultrasonic sensors have an internal or embedded temperature sensor to compensate for this effect.
This internal sensor measures the sensor body temperature, and the sensor corrects the temperature-related distortion of the measured values.
Be aware that internal temperature compensation sensors have limits. They may be affected by external heating or cooling sources, since they cannot adjust to extremely rapid changes well. They also may not be close to the temperature in the actual measurement path.
The orange line is the temperature of the sensor, changing by as much as 6°F. The red line shows the distance measurement fluctuating with temperature by at least 3-4 inches. The green line is the distance measurement with temperature compensation turned on in the sensor. As you can see, the measurements are stable and much more consistent.
Humidity
Humidity has negligible influence on the speed of sound at room temperature and at lower temperatures—up to a 0.036% / 10% RH change.
However, at higher air temperatures, humidity may increase—and with it, the speed of sound. This can have a negative effect on accuracy.
Due to an increase in relative humidity, some nitrogen and oxygen molecules of air are replaced by lighter molecules of water vapor.
As a result, molecular weight of air is decreased, which ultimately affects the speed of sound.
Air Pressure & Currents
The speed of sound decreases by less than 1% between sea level and 9,842 ft (3,000 m) altitude. Atmospheric fluctuations at a specific location are negligible. The effects on the speed of sound—and thus, ultrasonic technology—are hardly measurable.
Stormy weather with strong winds, air currents, or hurricanes can cause unstable measurements and a loss of signal.
Particularly hot objects—such as red-hot metal—cause significant air turbulence. The ultrasound echo can be scattered or deflected in such a way that no evaluable echo signal is returned.
Paint Mist
Paint mist has no detectable effect on the operation of ultrasonic sensors.
However, the mist should not be allowed to settle on the active transducer surface to avoid compromising the transducer’s sensitivity.
External Noise
External noise is distinguished from the desired target echoes and generally does not cause malfunctions. If the source of disturbance has the same frequency as the ultrasonic sensor, the level of the external noise must not exceed the level of the target echoes. Otherwise, this noise may interfere with the ultrasonic signal’s accuracy.
For example: filling a silo with stone. Compressed air jets also issue ultrasonic noise and can possibly interfere as well.
Types of Gas
Senix ultrasonic sensors are designed to operate accurately in atmospheric air.
However, operations in other gases such as carbon dioxide can cause serious measurement errors or even total loss of function due to deviations in the speed of sound and attenuation.
Tank Configurations & Dimensions
There are many tank types and shapes. These dimensions are crucial to understand for ideal ultrasonic accuracy.
Flat-bottom tanks or wells with straight sides are the easiest to calculate accuracy and capacity, as there is a linear relationship between tank level and volume. Irregular shaped tanks can be much more difficult to take into account and calculate.
External Reference Targets
For extreme changes in air temperature that require an even-faster response, the ToughSonic Reference Target Temperature Compensation (RTTC) accessory overcomes time lag that may occur with a built-in sensor. It also offers customers an improved and more accurate compensation option.
This system uses an external reference target, positioned at the front of the sensor and located in the measurement path. Combined with SensorView™ software, for each measurement, the sensor takes two readings: one to locate the reference target and one to the distant object. Any change in the speed of sound affects both measurements.
The reference target location is locked during calibration, and any change in its apparent position is applied proportionally to correct the distant object’s apparent location. The result is a more accurate measurement, unaffected by ambient air temperature, diurnal temperature swings, sensor self-heating, sunshine warming the sensor, cold ambient temperatures, or vibration.
Field calibrations and configuration can be done at any time or temperature.
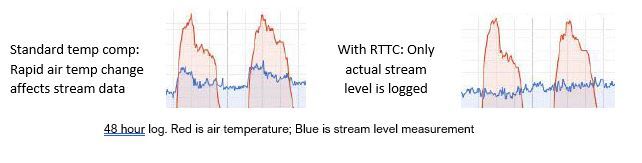
Figure 2: Sensors operating side by side over a canal, one with conventional temperature compensation (left) and one with RTTC compensation (right).
In the conventional, notice the apparent canal depth varies with extreme temperatures, while in the RTTC plot, notice the apparent distance is unaffected by temperature diurnal swings. The temperature effects have been largely eliminated.
While using temperature compensation, the diurnal temperature swings can be ignored, and external heating or cooling of the sensor will not result in incorrect distance or level measurements. The sensor can be exchanged on site, and a new calibration could be performed at any temperature.
The RTTC accessory improves a sensor’s performance in conditions with significant changes in temperature due to diurnal effects. The intensity of the diurnal changes and how the sensor software is configured will affect the sensor’s ultimate performance.
Ultrasonic accuracy specifications differ in their value. Overall, some are unclear as to the detailed conditions in which they were obtained. The most accurate ultrasonic sensors can achieve 0.1 – 0.2% of the detected range under perfectly controlled conditions, and most good ultrasonic sensors can generally achieve between 1% and 3% accuracy.
When selecting an ultrasonic sensor where accuracy is important, be sure to not only consider its published accuracy specifications, but also if it has built-in temperature compensation controls. If using the sensor outdoors, see if the manufacturer has an option for temperature compensation such as a reference target adaptor.
Have more questions? Contact the Senix team for support today.