Temperature Compensation Help
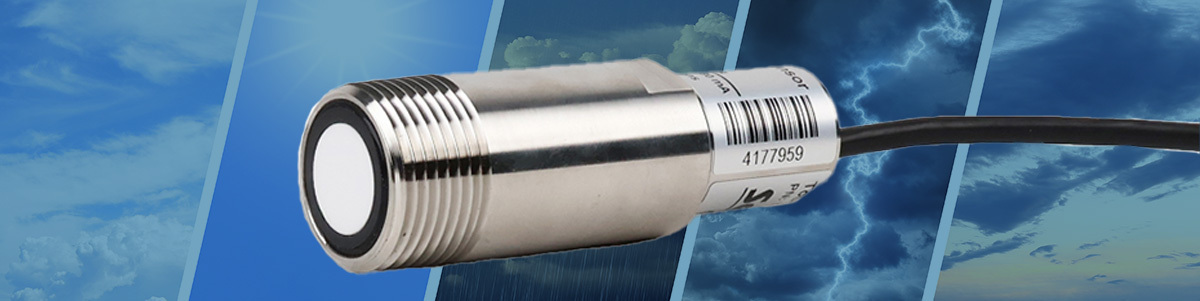
Air is an elastic medium, meaning the speed of sound varies with temperature and humidity—with temperature being the dominant factor. Measurements conducted by ultrasonic sensors are affected by these variables.
Senix ToughSonic® sensors use two methods to correct their measurements according to these environmental factors.
The speed of sound is nominally specified in dry air at 20°C (68°F), at 343 meters per second (1,125 ft/sec), which equates to approximately 768 mph.
This reduces to approximately 660mph at 30,000’ where the temperature is about -55°C.
Senix sensors are nominally accurate at 20.5°C (69.8°F), and speed of sound at 343.63 meters (1,127.4 ft/sec).
The speed of sound changes about 1% for each 10°F shift in temperature, and this shift must be considered in ultrasonic measurements.
As the temperature drops, the air becomes denser and sound travels faster. The faster sound travels, the shorter measured distances will appear if some means of temperature compensation is not applied.
Senix's Temperature Compensation Tools
Senix ToughSonic sensors incorporate temperature compensation circuitry that can be enabled or disabled using SensorView™ software.
Because of the wide variety of applications for distance and level measurement—as well as the possibility of dynamic changes in the measurement environment, where precision measurement is required—some testing is needed during installation.
Temperature compensation within the sensor will accommodate sensor body temperature changes but may not react quickly enough to shifts in the column of air through which the sensor is measuring.
This is particularly true where the sensor mounting technique provides thermal isolation from the ambient environment.
For cases where thermally generated errors are significant or measurement accuracy is required, Senix has implemented a Reference Target Temperature Compensation (RTTC). Plus, each new release of SensorView contains improved features to maximize the performance of the reference target accessory.
In this case, the reference target is positioned at a known, fixed distance from the sensor. The sensor first measures the reference target, then the unknown target, and factors the unknown distance proportional to shifts in the perceived position of the reference.
So long as the air within the measurement path is uniform, variations due to temperature are substantially reduced. This technique is particularly valuable where there may be rapid temperature shifts in the air.
Humidity's Role in Temperature Compensation
There are still potential problems with this technique. For example, in a tank, where there is no natural stirring of the air, it is possible for the upper and lower portions of the air to be at somewhat different temperatures. Temperature compensation will introduce errors for which the reference target approach cannot compensate.
Humidity changes produce only a very slight shift in the speed of sound.
As the amount of water vapor increases in the gas mixture of the air, the mean molecular mass of the air DECREASES. This may seem counterintuitive, but consider that air is mostly nitrogen (molecular mass 28), while H2O has a molecular mass of 18.
At 20°C, 1 atmosphere pressure, and 0% humidity, sound will travel at 343.36 meters/second. Increasing humidity to 50% raises that to 343.99 m/sec, while 100% humidity raises it to 344.62 m/sec. Thus, the variation from 0% to 100% humidity is approximately 0.36% of measurement.
Because humidity changes are usually accompanied by temperature changes, they are partly accommodated by temperature compensation techniques.
ToughSonics Maintain Accuracy in Varied Temperatures
Measurement accuracy for Senix sensors are typically anticipated on the order of <0.2% of measured distance. (Distinct from resolution, which is .086mm, or .00338”)
Note that we do not specify quarter percent accuracy due to the wide variety of environmental variables which might impact ultrasonic measurements.
SensorView software enables users of ToughSonic sensors to chart and statistically evaluate sensor signals, plus optimize their configuration. Measurement time, input filtering, signal averaging, transmit power, and receive gain are all adjustable by the user.
The result is superior measurement performance over non-computer configurable models.
For details on how to configure your reference target accessory, visit Senix’s guide here.