How Do Ultrasonic Sensors Work?
So you know about ToughSonic® ultrasonic sensors, but you want to learn how the technology functions. You're in the right place!
"Ultrasonic" refers to signals that are above the human hearing span (>20 kHz). There are several types of ultrasonic transducers. Industrial ultrasonic sensors that measure through air generally transmit between 30–500 KHz. As the ultrasonic frequency increases, the rate of attenuation increases. Thus, low-frequency sensors (30–80 kHz) are more effective for long range, while high-frequency sensors are more effective for short range.
Higher frequency sensors (80–500 kHz) also reduce the ringing-decay, which allows for a shorter minimum detection range.
Most ultrasonic sensors, for testing purposes—such as for non-destructive (NDT) testing—transmit at higher frequencies, generally between 1–10 MHz. Ultrasonic sensors for medical ultrasound applications are also higher in frequency and transmit generally in the 1 MHz–20 MHz range for imaging purposes, and below 2 MHz for therapeutic purposes.
Wherever non-contact distance measurement is desirable, industrial ultrasonic sensors with the frequency range of 30–300 KHz are used. These types of ultrasonic sensors—sometimes called ultrasonic transducers—measure the distance to or the presence of a target object by sending a sound pulse toward the target, then measuring the time it takes the sound echo to return.
Knowing the speed of sound, the sensor determines the distance of the target and sets its outputs accordingly. If the temperature changes or fluctuations are present, some ultrasonic sensors can automatically apply an offset scaling for temperature compensation.
Applications fall into three general categories:
Liquid Level 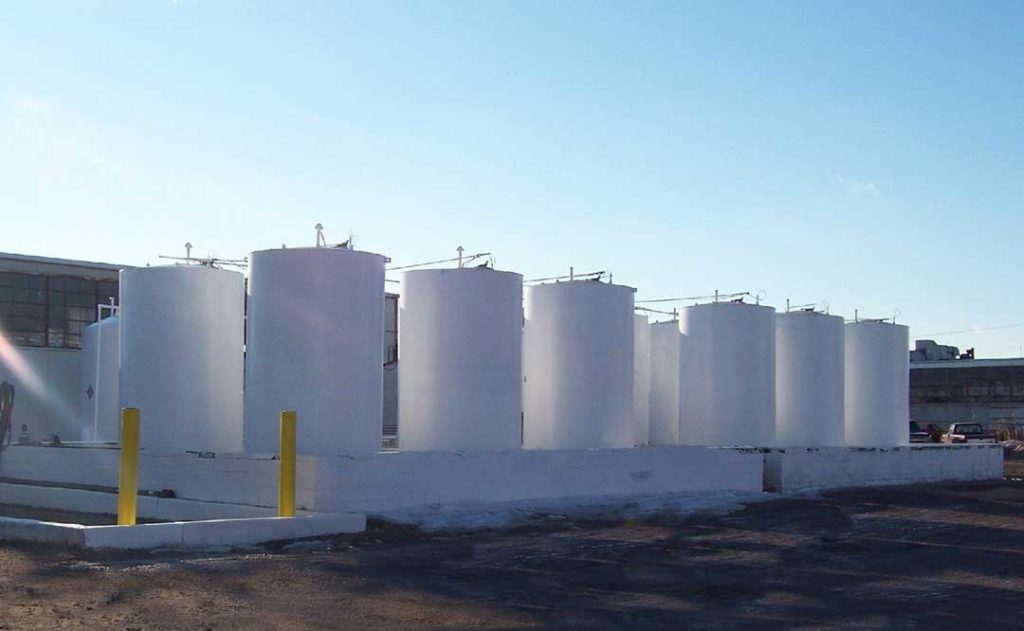
- Tank Level – Liquids and solids in open and closed tanks
- Water Monitoring – For conservation, efficiency, and safety
- Water Management – Monitoring levels in streams, canals, channels, and ponds
- Liquid Flow – Measuring liquid height in flumes, weirs, and channels to calculate volumetric flow of water and eluents
- Flood & Tsunami Warnings – Monitoring levels of streams or bodies of water to warn communities
- Fuel Monitoring – For inventory of fuel, usage, theft
Distance Ranging & Dimensional
- Roll Diameter – Paper, film, or foil to identify web tension or amount remaining on a roll
- Loop Control – Measuring the free loop of material as it is being moved from one machine to another to prevent breakage
- Height & Size – Objects such as boxes, containers, etc.
- Positioning – The position of an object can be used in a closed loop system to maintain or control position
Object Detection or Proximity Detection
- Objects can be detected for security, counting, inventory or robotic obstacle avoidance
- People can be detected at kiosks or determined to be approaching or leaving
- Targets can be monitored over the full sensor range or restricted within user-defined distance ranges
- Used for longer-range applications for detection, presence, or absence of objects or materials
Industrial ultrasonic sensors will detect both large and small targets, including liquids, solids and granular materials. The size, shape, and orientation of the target will affect the maximum distance at which it can be detected. The sensor is not affected by optical characteristics such as color, reflectivity, transparency, or opaqueness.
How Are Ultrasonic Sensors Used?
Need to know how much diesel fuel is in the tank, how high the water level is under the bridge, or whether the chicken feed will last longer than the chickens? Do you want to ensure the proper amount of water is fed to crops, monitor for theft or a spill from a tank? Is turning on a pump to refill a tank, or start a motor when the level gets to a certain point, or trigger an alarm?
Ultrasonic sensors are used in these and hundreds more applications. They are used with noisy machinery, including motor drives and other electrical and electromechanical controls. Non-contact ultrasonic sensors have distinct advantages in challenging environments where corrosive, scaling, coating, or dirty materials are likely to negatively impact the performance and maintenance costs of contact sensors. Non-contact ultrasonic sensors are also desirable where the material being measured cannot be corrupted by contact with any measuring device.
Temperature can affect an industrial ultrasonic sensor, but can be compensated for with the right sensor. Humidity change is generally not a significant factor (0.036% / 10% RH change). Normal atmospheric pressure changes—or small pressure changes in vessels—will not affect ultrasonic sensor operation either.
High-Quality Ultrasonic Sensors From Senix
Ultrasonic signals give autonomous, no-contact tools the ability to register nearby obstacles and surfaces. At Senix, we manufacture an array of ultrasonic sensors for use across different industries and applications. For assistance with selecting the right ultrasonic sensor for your needs, check out our selection guide.
For more information on how Senix can help with your application, contact us at info@senix.com or click here.